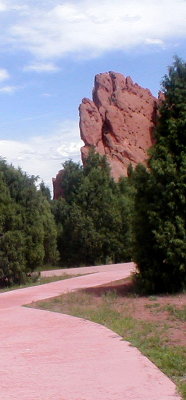
|
MullaneyVision Highlights of Six Sigma
This page is offered to the community as a summary of concepts related to Six Sigma. If you are wondering what Six Sigma is or how to explain it to others, perhaps the resources on this page will be of interest. Six Sigma is both the measure and the mindset of nearly eliminating errors in production.
The summary is divided to address the following questions:
This website has been heavily
inspired by PMI and AVR Associates, Limited.
|
focus here
| return to top of this page
|
What is Six Sigma?
Six Sigma is a measure and an approach to quality and reliability of products or work. Sigma is the the Greek letter (σ) used to measure statistical variance; any work or quality that can be measured should tend to produce a focus in the results. This focus is usually measured as the mode or mean (average) of the measured data. Variation always occurs, so a significant amount of data points occur on either side of the focus. As the distance from the focus increases, the occurence of data points decreases; this standard behavior is referred to as a normal distribution. Standard deviation is a statistical tool used to characterize the distance from focus. Sigma is essentially the square root of the variance.
|
Related Links
|
Origin
The American company Motorola developed Six Sigma (in 1986) to standardize the way defects were counted and to improve business performance. The company web page shares these insights: "Six Sigma provided Motorola the key to addressing quality concerns throughout the organization, from manufacturing to support functions. The application of Six Sigma also contributed to Motorola winning the Malcolm Baldrige National Quality award in 1988.
Since then, the impact of the Six Sigma process on improving business performance has been dramatic and well documented by other leading global organizations, such as General Electric, Allied Signal, and Citibank. That's why investing in Six Sigma programs is increasingly considered a mission-critical best practice, even among mid-sized and smaller firms."
Why 6?
A single sigma (standard deviation) covers about 68% of data samples (34.1% on either side of the mean) in a normal distribution. Moving out to the next step (2σ) expands the coverage to greater than 95%. As more steps are taken from the mean, the coverage grows to more than 99.999% at 6σ. If you were tracking defects per million opportunities, this would allow only 3.4 DPMO. That was Motorola's target.
Some Vocabulary
Two methodologies' names serve as good vocabulary introductions. DMADV works best for introducing quality systems to new environments:
- Define goals of the design activity
- Measure and identify areas critical to quality
- Analyze competing designs
- Design down to details; optimize
- Verify design; set up pilot runs
DMAIC works best to improve existing business processes:
- Define process improvement goals
- Measure baseline data from existing process(es)
- Analyze causality of relationship
- Improve process using formal techniques
- Control variance levels to prevent defects
|
focus here
| return to top of this page
|
Why?
Six Sigma is more than a measure. It is a corporate mindset about fortifying for possible weakness and eliminating wasted effort. If your company is interested in saving money, improving quality and meeting industry standards, you would do well to consider investing in Six Sigma methodologies.
|
Related Links
|
Save Money
Charles Waxer was not satisfied with the standard reports of Six Sigma savings:
- "Companies of all types and sizes are in the midst of a quality revolution. GE saved $12 billion over five years and added $1 to its earnings per share. Honeywell (AlliedSignal) recorded more than $800 million in savings."
- "GE produces annual benefits of over $2.5 billion across the organization from Six Sigma."
- "Motorola reduced manufacturing costs by $1.4 billion from 1987-1994."
- "Six Sigma reportedly saved Motorola $15 billion over the last 11 years."
He went on to investigate what the companies reported in their financial statements. The results show that Six Sigma savings as a percentage of revenue range from 1.2% to 4.5%. He also quoted GE as estimating that average quality (as opposed to Six Sigma levels) cost companies 10-15% of their revenue.
Improve Quality
Thomas Pyzdek wrote on QualityAmerica.com: "For Six Sigma purposes I define quality as the value added by a productive endeavor. Quality comes in two flavors: potential quality and actual quality. Potential quality is the known maximum possible value added per unit of input. Actual quality is the current value added per unit of input. The difference between potential and actual quality is waste. Six Sigma focuses on improving quality (i.e., reducing waste) by helping organizations produce products and services better, faster and cheaper. In more traditional terms, Six Sigma focuses on defect prevention, cycle time reduction, and cost savings."
Industry Standard
One consulting group published this report: "Across many industries and many types of projects, Six Sigma Systems team members have delivered results such as these:
- A $2 M reduction in inventory for one product line.
- A $3.5 M savings through improved quality of critical component.
- A $11 M gain from inventory reduction, cycle time reduction and increased sales."
|
focus here
| return to top of this page
|
Which?
Legend tells us that the original team at Motorola realized that "process characterization experts" did not convey the excitement of change associated with Six Sigma proponents. They adopted some terminology of the martial arts to emphasize progression and top-knotch professionalism.
|
Related Links
- avrassociates.com,
AVR Associates, Ltd. provides training and certification related to Six Sigma (and heavily influenced the content of the page you are reading)
- www.motorola.com, Motorola's Six Sigma Dictionary and links to Motorola University
- isixsigma.com iSixSigma, a magazine with articles, instruction and tools
- www.iil.com/leansixsigma, International Institute for Learning, Inc.
- www.6sigmastudy.com,
6 Sigma Study is a Registered Education Provider with PMI
- www.isssp.com,
International Society of Six Sigma Professionals
- www.pmi.org, contact your local chapter of the Project Management Institute for related training or networking
- mabpmp.com,
the professional page of this Six Sigma enthusiast
|
Yellow Belt
AVR Associates describes the introductory training: "...The entry level into the Six Sigma discipline is the Yellow Belt, which is designed to provide a general orientation and prepare individuals to recognize and meaningfully participate in Six Sigma efforts.
..."
Green Belt
AVR Associates also offers a Green Belt course (80-90 instructional hours) which includes these objectives:
- "Recognize key attributes of a successful Six Sigma program
- Appreciate project selection criteria
- Realize the role of a Green Belt in the Six Sigma organization
- Understand fundamentals of the DMAIC problem solving methodology
- Use basic Six Sigma tools for Six Sigma project definition and process baseline
- Understand the need for advanced problem-solving and improvement methodologies used by Project Teams
- Actively participate in a Six Sigma team"
Black Belt/Master
Black Belt and Master Black Belt levels require an entire corporate environment investing in Six Sigma. Professionals such as Doug Lowe lead efforts within those companies. They ensure and execute the best practices of Six Sigma as applicable to their business goals. The Master BBs focus on training of Green Belts and Black Belts in addition to strategic selection of Six Sigma projects.
Champion/Executive Leader
The iSixSigma article by Mike Carnell and Scot Shank offers a rather colorful image of Six Sigma champions:
"One critical characteristic for successful Six Sigma Champions is that they are some hybrid of Henry Kissinger and Xena, the Warrior Princess. It may actually be easier to find the mutant offspring of these two leaders than it is to find the complete Champion. Being the complete Champion requires more than diplomatic and warrior skill sets. Champions must be proficient in four other areas:
- Business and operations interface
- Project selection
- Pace mediation
- Results implementation"
The authors also point out that "Champions should remove roadblocks. Champions need to be in a position to defuse any issues that may arise between a Black Belt and another person in the organization, particularly if the issue is with someone with a higher formal position in the company. The Champion should be the buffer that keeps a Black Belt out of a head-to-head confrontation with Managers, Vice Presidents and Directors in the company, allowing Black Belts the freedom to focus on the problem, not engage in some inane territorial dispute. This is the most fundamental function of the Champion."
|